DOT-FAA-AR-99-49
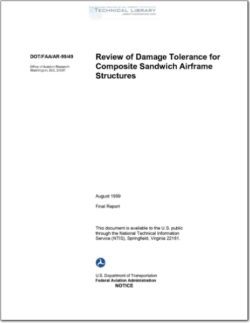
- Version
- 645 Downloads
- 1.42 MB File Size
- 1 File Count
- March 24, 2016 Create Date
- March 24, 2016 Last Updated
Review of Damage Tolerance for Composite Sandwich Airframe Structures
The use of composite sandwich construction is rapidly increasing in current and future airframe
designs especially for general aviation aircraft and rotorcraft. Typically, sandwich constructions
in these applications use thin-gage composite facesheets (0.020” to 0.045”) which are cocured to
honeycomb and foam cores. Due to the nature of these structures, damage tolerance is more
complex than conventional laminated structures. Besides typical damage concerns such as
through penetration and delamination, additional modes including core crushing and facesheet
debonding must also be addressed. This complicates the certification process by introducing
undefined Allowable Damage Limits (ADL) and Critical Damage Thresholds (CDT) as related to
the ultimate and limit load-carrying capability of the structure.
This document provides a background review of previous damage tolerance investigations
including an overview of traditional metallic damage tolerance methodologies. Illustrative
summaries are presented which show the scope of previous investigation parameters such as
impact energy, facesheet thickness, and core thickness of typical sandwich constructions. Also
included is a compilation of damage tolerance certification procedures and regulations taken
from FAR Part 23-29 for composite damage tolerance as well as recommendations from
associated Advisory Circulars.
Past and current airframe industry sandwich constructions which show the scope of current and
future sandwich designs were also surveyed. In conclusion, a proposed future research approach
and its methodology are presented which should aid in establishing certification guidelines and
confidence involving the damage tolerance of sandwich constructions, particularly as they apply
to general aviation aircraft and rotorcraft.
Sandwich structures provide an efficient method to increase bending rigidity without a significant
increase in structural weight. Thin-gage facesheets (0.020" to 0.045") are cocured or bonded to
honeycomb (aluminum or Nomex) or syntactic foam cores. Thus, structures, based upon a
minimum gage thickness adequate to carry the in-plane loads, can be made to carry out-of—plane
loads and to be stable under compression without a significant weight penalty. The potential of
sandwich structures is substantial. Helicopter blades, optical benches for space applications, and
nonferrous ship hulls are some of the current applications. In general aviation, skin/stiffener
structures can be replaced with sandwich structures. Design is based on several loading regimes
including pressurization, gust, and landing loads. Sandwich construction figures prominently in
future aerospace applications such as Raytheon’s Premier I, Lockheed-Martin’s X-33, and future
tilt rotors by Boeing Defense & Space Group, Helicopters Division.
File | Action |
---|---|
DOT-FAA-AR-99-49 Review of Damage Tolerance for Composite Sandwich Airframe Structures.pdf | Download |
Comment On This Post