NASA-CR-4608
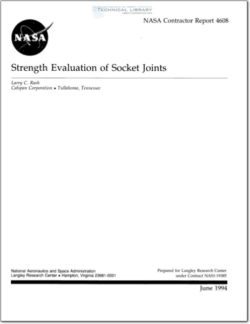
- Version
- 1067 Downloads
- 1.35 MB File Size
- 1 File Count
- November 27, 2015 Create Date
- November 27, 2015 Last Updated
Strength Of Socket Joints
INTRODUCTION
The results included in this report were previously released as a company report, see Reference 1, and
this report is intended to formalize that analysis and to document the results of a validation study that
was performed later and included here as Appendix B. Prior to that analysis, the stresses in the joints
of the model support systems were resolved by assuming the moment in the joint was reacted about
the center of the joint and the stresses were the result of this moment that were reacted over a plane
parallel to the horizontal centerline. The new analytical technique was developed to better define the
loads and stresses in typical sting joints found in the model support systems at the National Transonic
Facility at NASA LaRC and to provide a design tool that could easily be used during the design of new
model support systems. To be more precise, the original objective was to provide a method of
determining the loads and stresses in concentric, tapered, socket type joints found in wind tunnel model
support systems. Once completed, the analytical method was found to be applicable to any
overlapping type joint. Some joints for which the method is applicable are illustrated in Figure 1 and
includes general configurations where one of the joint members can be considered to be basically
supported by the contact pressure from the other joint member. The forward end of a model support
system engages with and is supported by an aft support system, which is the subject of this report. A
lamppost is supported by the ground and the analytical technique included herein can be used to
determine if the depth of penetration is sufficient for the bearing pressure of the soil to laterally
support the lamppost during high wind conditions. The strength of a clamped round bar assembly and
the strength of a tongue and groove type joint that are subjected to external forces and moments can
both be evaluated using this analytical technique. The tongue and groove joint would, however,
require some additional development to determine the proper stress relationships which could be
accomplished by a similar analysis to what is included here by using strip theory to evaluate the
strength of a unit width of the joint.
The results in this report are in the form of equations that are for a concentric, tapered socket type
joint and can be used during the design of new model support systems to determine the strength of
socket joints and for most applications the need of more lengthy analyses can be avoided. Results are
provided for both a joint where the joint members are in continuous contact along the full length of
the joint and for a joint with intermediate contact relief. The joint with intermediate contact relief has
a gap between the joint members along about one—third of the midsection of the joint, typical of
NASA LaRC sting joints, and the joint members are in full contact fore and aft of this midsection gap.
Illustrations of both joint types are given in Figures 2 and 3. Analytically, the approach for both was
to use Strength of Materials principles to analyze the joint members by idealizing the joint as two
rigid, parallel beams that are joined by an infinite number of springs along the contacting surfaces.
The contact loads can be pictured as being equivalent to the loads developed in the springs along the
length of the joint attributed to the differential slope between two rigid joint members. The contact
loads between the joint members are represented as externally applied, linearly varying, distributed
loads and are as shown on the free body diagrams in Figure 2 and 3. Each joint member is treated like
a simple beam and the contact loads between the beams are taken to act like external loads that are
independently applied to each of the two beams. For the first joint member, depicted in Figures 2b
and 3b, the externally applied loads are balanced by the application of the contact type loads and for
the second joint member, depicted in Figures 2c and 3c, the contact loads are the only loads that act
on the end of the cantilevered beams. These contact loads, in conjunction with the externally applied
loads for the forward joint members are used to develop independent expressions for the bending
moment along the length of the joint for the two joint members. The joint stress relationships for the
joint members are determined from the bending moment equations by including the effects of
appropriate section properties for a given geometry. The geometry of the contacting surfaces for the
joint in this report is in the shape of a frustum of a cone and is representative of the tapered socket
type joints found in model support systems in NASA LaRC wind tunnels.
The results in this report can be used to determine the distributed contact loads and stresses in sting
joints directly from joint dimensions and externally applied loads. As a design aid, the key equations
have been programed for a personal computer to automatically compute all the results given in this
report. A copy of an IBM BASIC program that was developed to evaluate the results for a concentric
tapered, socket type joint is included as Appendix A.
File | Action |
---|---|
NASA-CR-4608 Strength of Socket Joints.pdf | Download |
Comment On This Post