DOT-FAA-AR-01-33
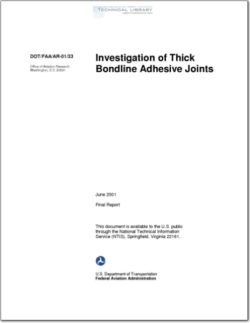
- Version
- 629 Downloads
- 8.21 MB File Size
- 1 File Count
- March 24, 2016 Create Date
- March 24, 2016 Last Updated
Investigation of Thick Bondline Adhesive Joints
In recent years, the use of polymer matrix composite materials as primary structural components
has risen, especially in the general aviation (GA) industry. The use of composites not only
results in weight savings, but also reduces part counts, joining operations, and results in
significant savings in assembly, storage, and inspection. However, joining of some integral parts
is still required. GA aircraft industry also uses bonded joints with bondline thicknesses much
greater than the 0.01in. that was standard in aircraft bonded joints. For composites, there are two
methods of joining: bonding and mechanical fastening. Of the two, adhesively bonding
composite structures is the preferred method for a variety of reasons. There are several adhesive
test methods that are used to determine the in situ properties of an adhesive joint for use in
design. From these methods, ASTM D 1002, D 3165, and D 5656 were evaluated in this
investigation with the substrate materials of 2024—T3 phosphoric anodized aluminum,
carbon/epoxy quasi-isotropic laminate, and fiberglass/epoxy quasi—isotropic laminate.
Bondline thicknesses from 0.010-0.l60 inch were evaluated for three paste adhesive systems using
different test methods and substrate materials. The apparent shear strength given by the test
methods investigated was found to be highly dependent on adherend bending stiffness, which
directly effects the peel stress distributions in the adhesive layer. Thin-adherend specimens,
regardless of bondline thickness, yielded lower apparent shear strengths than the thick adherend
specimens and gave misleading information when comparing the apparent shear strengths of
different adhesive systems. The adhesive shear-stress behavior was characterized over the range
of bond thicknesses and environmental conditions and several recommendations and correction
factors were offered for the thick-adherend test method.
Due to reformulations in the base adhesives and the low glass transition temperatures, which
were found during this study, the adhesives investigated in the report may not be representative
of the current adhesive formulations used in production of GA aircraft. However, the adhesive
mechanical properties reflect the correct trends for the effect of adhesive thickness and
environment.
File | Action |
---|---|
DOT-FAA-AR-01-33 Investigation of Thick Bondline Adhesive Joints.pdf | Download |
Comment On This Post