naca-report-477
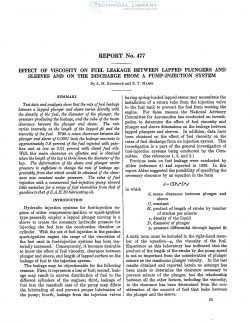
- Version
- 179 Downloads
- 1.27 MB File Size
- 1 File Count
- August 26, 2016 Create Date
- August 26, 2016 Last Updated
National Advisory Committee for Aeronautics, Report - Effect of Viscosity on Fuel Leakage Between Lapped Plungers and Sleeves and on the Discharge from a Pump Injection System
Test data and analysis show that the rate of fuel leakage
between a lapped plunger and sleeve varies directly with
the density of the fuel, the diameter of the plunger, the
pressure producing the leakage, and the cube of the mean
clearance between the plunger and sleeve. The rate
varies inversely as the length of the lapped fit and the
viscosity of the fuel. With a mean clearance between the
plunger and sleeve of 0.0001 inch the leakage amounts to
approximately 02 percent of the fuel injected with gaso-
line and as low as 0.01 percent with diesel fuel oils.
With this mean clearance an effective seal is obtained
when the length of the lap is three times the diameter of the
lap. The deformation of the sleeve and plunger under
pressure is suficient to change the rate of leakage ap-
preciably from that which would be obtained if the clear-
ance was constant under pressure. The rates of fuel
injection with a commercial fuel-injection pump showed
little variation for a range of fuel viscosities from that of
gasoline to that of S.A.E. 30 lubricating oil.
Hydraulic injection systems for fuel-injection en—
gines of either compression-ignition or spark-ignition
type generally employ a lapped plunger moving in a
sleeve to create the necessary hydraulic pressure for
injecting the fuel into the combustion chamber or
cylinder. With the use of fuel injection in the gasoline
spark—ignition engine the range of the viscosities of
the fuel used in fuel-injection systems has been ma-
terially increased. Consequently, it becomes desirable
to know the effect of fuel viscosity, clearance between
plunger and sleeve, and length of lapped surface on the
leakage of fuel in the injection system.
The leakage may be objectionable for the following
reasons: First, it represents a loss of fuel; second, leak-
age may result in uneven distribution of fuel to the
different cylinders of the engines; third, leakage of
fuel into the camshaft case of the pump may dilute
the lubricating oil and prevent proper lubrication of
the pump; fourth, leakage from the injection valves
having spring—loaded lapped stems may necessitate the
installation of a return tube from the injection valve
to the fuel tank to prevent the fuel from wetting the
engine.
File | Action |
---|---|
naca-report-477 Effect of Viscosity on Fuel Leakage Between Lapped Plungers and Sleeves and on the Discharge from a Pump Injection System.pdf | Download |
Comment On This Post