NASA-CR-3875
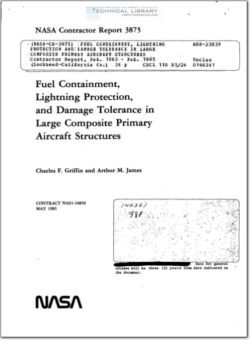
- Version
- 237 Downloads
- 25.21 MB File Size
- 1 File Count
- May 19, 2016 Create Date
- May 19, 2016 Last Updated
Fuel Containment and Lightning Protection Composite Aircraft Structures
SUMMARY
This program was conducted to identify and resolve technical problems
associated with fuel containment and damage tolerance of composite material
wings for transport aircraft. The major tasks within the program were:
0 The preliminary design of damage tolerant wing surfaces using
composite materials
0 The evaluation of fuel sealing and lightning protection methods for
a composite material wing
o Tests of a composite wing panel designed to meet transport aircraft
requirements
0 An experimental investigation of the damage—tolerant characteristics
of toughened resin graphite/epoxy materials.
Preliminary design studies predict that compared to the aluminum baseline,
wing surfaces constructed with graphite/epoxy composites offer significant
weight savings if design allowable strains can be increased from the current
levels. Tests on laminates fabricated with high strain-to—failure graphite
fibers combined with currently available tougher resins indicate that higher
strain allowables for tension can be obtained. For greater post-impact com—
pression strength, significant material improvements are desirable.
Based on tests conducted in this pregram, it is concluded that the con—
ventional fuel tank sealing techniques used for joints in metal structures are
equally applicable to composite structures. The fuel containment capability
of a graphite/epoxy tank could be compromised by low energy impact damage;
however, it has been determined that a 0.005—inch thick coating of a flexible
polyurethane paint on the inside of the wing skin would prevent fuel leaks due
to low-energy impact damage.
Swept—stroke lightning strikes to unprotected graphite/epoxy stiffened
panels caused internal sparking and a large amount of structural damage. A
surface protection material consisting of a graphite/aluminum wire fabric and
.a fastener treatment of polysulfide and a plastic cap proved effective in
eliminating arcing and reducing structural damage.
The technology developed in this program was demonstrated by the fabrica-
tion and test of a blade-stiffened wing cover section including the spar-to-
cover and rib-to-cover joints. 'The specimen test results exceeded design
requirements for all test conditions.
File | Action |
---|---|
NASA-CR-3875 Fuel Containment and Lightning Protection Composite Aircraft Structures.pdf | Download |
Comment On This Post