NASA Paper N95-28841
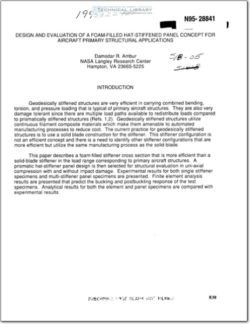
- Version
- 198 Downloads
- 1.09 MB File Size
- 1 File Count
- December 13, 2015 Create Date
- December 13, 2015 Last Updated
Design and Evaluation of a Foam Filled Hat Stiffened Concept
Geodesically stiffened structures are very efficient in carrying combined bending,
torsion, and pressure loading that is typical of primary aircraft structures. They are also very
damage tolerant since there are multiple load paths available to redistribute loads compared
to prismatically stiffened structures (Refs. 1,2). Geodesically stiffened structures utilize
continuous filament composite materials which make them amenable to automated
manufacturing processes to reduce cost. The current practice for geodesically stiffened
structures is to use a solid blade construction for the stiffener. This stiffener configuration is
not an efficient concept and there is a need to identify other stiffener configurations that are
more efficient but utilize the same manufacturing process as the solid blade.
This paper describes a foam-filled stiffener cross section that is more efficient than a
solid-blade stiffener in the load range corresponding to primary aircraft structures. A
prismatic hat-stiffener panel design is then selected for structural evaluation in uni-axial
compression with and without impact damage. Experimental results for both single stiffener
specimens and multi-stiffener panel specimens are presented. Finite element analysis
results are presented that predict the buckling and postbuckling response of the test
specimens. Analytical results for both the element and panel specimens are compared with
experimental results.
In order to make the solid-blade stiffener shown in Figure 1 more efficient, if is
necessary to position the 0° material away from the skin to increase the bending stiffness.
When such a stiffener concept is applied to a geodesically stiffened structural configuration,
the tooling design becomes extremely complicated if the tooling must be removed after
curing. It is cost effective to leave the tooling in the hat stiffener if the material for the tool is
light in weight and has the necessary processing characteristics for curing and adequate
mechanical properties to support the stiffener and skin elements when loaded. In a typical
manufacturing process, the overvvrap material is first placed in a female tool and
unidirectional material is tow placed to form a predominantly 0° material stiffener cap. A pre-
machined foam insert is then placed in the tool to complete the stiffener. Skin material of the
required thickness is then tow placed to complete the assembly which is then cured to
produce the geodesically stiffened structure. As a first step toward evaluating this stiffener
concept for geodesically stiffened structures, a prismatic stiffener panel study was undertaken
which is the subject of this paper.
File | Action |
---|---|
NASA Paper N95-28841 Design and Evaluation of a Foam Filled Hat Stiffened Concept.pdf | Download |
Comment On This Post