NASA-TM-101133
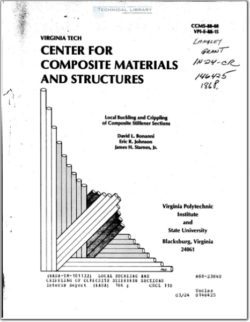
- Version
- 260 Downloads
- 28.80 MB File Size
- 1 File Count
- November 27, 2015 Create Date
- November 27, 2015 Last Updated
Local Buckling And Crippling Of Composite Stiffener Sections
The reduction of structural weight is of great concern to an aerospace vehicle designer. Weight
pared from the structure creates the desirable alternatives of increased payload capacity or a de-
creased need for propulsive energy. For this reason, aerospace vehicle structures are usually of the
semimonocoque type; that is, they have a stiffened, thin shell configuration. This method of con-
struction combines thin-sheet coverings or skins with longitudinal stiffener members and transverse
support elements. Incorporation of laminated composite materials into such a design offers further
weight savings, due to the high strength-to-weight and stiffness-to-weight ratios of these materials.
Proper attachment between skin and stiffeners is vital if the system is to perform effectively. Me-
tallic components are commonly joined by closely spaced mechanical fasteners. Composite
stiffeners may be bonded, stitched, co-cured, or mechanically fastened to the skin. In any case, the
connection between skin and stiffener is continuous or nearly continuous. The stiffeners themselves
are thin-walled, prismatic structural elements consisting of flanges and webs; some of the more
common open shapes are angles, blades, zees, channels, and I- and J -sections.
Compressive loading of a stiffened skin structure may cause loss of stability. Stiffened-skin panels
are usually designed so that the skin buckles in compression before the stiffeners. As a conse-
quence, the compressive load increases more rapidly in the stiffeners than in the postbuckled skin
as the total compressive load on the panel is increased. For co-cured or secondarily bonded com-
posite stiffeners, catastrophic panel failure may be initiated either by stiffener separation from the
skin (also known as stiffener pull-off) or by local buckling and then crippling of the stiffener section.
It is assumed in the present work that the stiffened panel design is such that the stiffener pull-off
mode of failure does not occur prior to crippling.
Local buckling of a stiffener is characterized by the buckling of flange and web elements as separate
plates which rotationally restrain each other at the element junctions, or comers. The comers
themselves can remain straight and parallel. Thus, the cross section of the stiffener deforms, but
does not rotate or translate. This may be distinguished from a global or overall buckling mode,
common to long columns, in which the cross section of the column rotates and/or translates, but
does not distort. Since local buckling is essentially a plate buckling phenomenon, these stiffeners,
like buckled plates restrained along at least one unloaded edge, have postbuckling strength. Even-
tual failure of the stiffeners in the postbuckled state is known as stiffener crippling.
File | Action |
---|---|
NASA-TM-101133-local-buckling-and-crippling-of-composite-stiffener-sections.pdf | Download |
Comment On This Post