NASA-TM-2010-216876-ARL-TR-5121
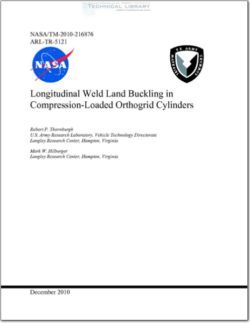
- Version
- 263 Downloads
- 1.07 MB File Size
- 1 File Count
- April 21, 2016 Create Date
- April 21, 2016 Last Updated
Longitudinal Weld Land Buckling in Compression-Loaded Orthogrid Cylinders
Stiffened and unstiffened shells are very common in the structural design of aerospace vehicles and
almost all other structures where weight is of primary concern. For these types of structures buckling is a
critical failure mode that must be taken into account during the design process. Although some shells can
buckle without catastrophic failure of the structure, many types of structures, such as large—diameter, thin—
walled LV cylinders, must be designed to completely prevent buckling. Such structures exhibit an
unstable buckling behavior in which the buckling event corresponds to a sudden loss in load-carrying
capability. It is the design and analysis of this class of structures that is the topic of discussion in this
paper.
lntegrally stiffened metallic cylinderical shell structures are an efficient design choice for LVs because
their stiffness and strength can easily be tailored to create an optimal design for a given loading condition.
Although stiffeners can be arranged in any arbitrary pattern, typically designers use either an isogrid
arrangement [ref 1], with the stiffeners forming equilateral triangular bays, or an orthogrid arrangement
[refs 2—6], with the stiffeners forming rectangular bays. The orthogrid arrangement is considered in this
work, but the response of isogrid stiffener structures is fundamentally similar to the response of orthogrid
structures. The fact that the stiffeners are integrally machined results in a reduction in stress
concentrations and improved structural quality. By using metallic materials such as aluminum alloys,
structural components can be welded together to form large structures such as liquid hydrogen tanks.
However, in order to create the integrally stiffened cylinders needed to form most liquid fuel tanks, which
are often 8 to 33 feet in diameter, multiple curved panels must be welded together along their longitudinal
edges to form a single barrel component. Thus, the assembled structure is not a continuously stiffened
shell, but rather a segmented shell with discontinuities created by the weld lands. The length and arc-
width of the panels used is governed by size of plate stock available for a given thickness, and often
multiple barrels must then be welded together to create cylinders with the desired length. In the current
state-of-the-art manufacturing process, panels are machined from flat plat stock to form the stiffeners on
the inner surface of a thin skin before the panels are formed to the correct cylindrical radius.
File | Action |
---|---|
NASA-TM-2010-216876-ARL-TR-5121 Longitudinal Weld Land Buckling in Compression-Loaded Orthogrid Cylinders.pdf | Download |
Comment On This Post