NASA-TP-1507
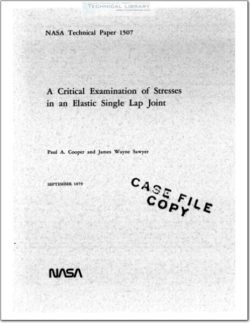
- Version
- 257 Downloads
- 15.15 MB File Size
- 1 File Count
- April 21, 2016 Create Date
- April 21, 2016 Last Updated
Stresses in an Elastic Single Lap Joint
The results of an approximate nonlinear finite—element analysis of a single
lap joint are presented and compared with the results of a linear finite-element
analysis, and the geometric nonlinear effects caused by the load-path eccentric-
ity on the adhesive stress distributions are determined. The approximate non-
linear finite—element solution is evaluated by comparison with a nonlinear solu-
tion obtained from a finite-difference analysis, and results are compared with
the classical approximate analysis by Goland and Reissner. An experimental pho—
toelastic study of the moment distribution in the lap_joint adherend is used to
evaluate the adequacy of plate approximations for analyzing single lap joints.
The results from finite—element, Goland-Reissner, and photoelastic analyses show
that for a single lap joint the effect of the geometric nonlinear behavior of
the joint has a sizable effect on the stresses in the adhesive. The Goland—
Reissner analysis is sufficiently accurate in the prediction of stresses along
the midsurface of the adhesive bond to be used for qualitative evaluation of the
influence of geometric or material parametric variations. Detailed stress dis-
tributions in both the adherend and adhesive obtained from the finite—element
analysis are presented to provide a basis for comparison with other solution
techniques.
Adhesively bonded joints offer the aerospace designer an attractive mass-
efficient alternative to the mechanical fastening of structural components.
(See, for example, ref. 1.) In the past, however, the poor reliability of
bonded joints has in general dissuaded designers from taking full advantage
of the projected benefits of bonded structural designs. Thus, growth in the
use of bonded systems in load—carrying canponents is not keeping pace with the
continuing development and improved reliability of new high-strength adhesives
(refs. 1 and 2). Bonded joints should be designed to transfer load in shear
with a minimum of peel across the bond line since adhesives are generally more
efficient in supporting shear forces and perform poorly when supporting peel-
type forces. Design of bonded joints thus requires knowledge of the shear and
peel stress distributions in the bond line as well as the shear strength of the
adhesive. The single lap joint (fig. 1) is the simplest joint which transfers
in—plane load primarily by shear in the adhesive. In fact, the ASTM D 1002—72
single-lap—joint test (ref. 3) is the most pepular experimental procedure for
evaluating the shear strength of adhesives.
File | Action |
---|---|
NASA-TP-1507 Stresses in an Elastic Single Lap Joint.pdf | Download |
Comment On This Post