NASA-TP-2935
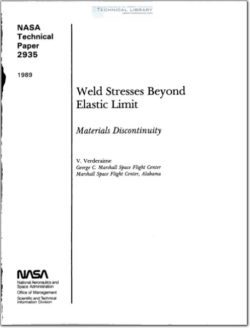
- Version
- 329 Downloads
- 820.29 KB File Size
- 1 File Count
- March 6, 2016 Create Date
- March 6, 2016 Last Updated
Weld Stresses Beyond the Elastic Limit
Many spacecraft structures are required to be verified with a minimum safety factor of 1.] on
yield and I .4 on ultimate strength [I] which, in the design phase, are both conservatively complied with
in a linear fashion [2]. As the structure progresses through the operational phase and prevailing environ-
ments begin to exceed original design requirements, safety demands that current margins be affirmed.
Determination of post—development safety factors on yield are linear and are usually accommodated, but
ultimate strength predictions involve nonlinear considerations not commonly understood. The intent of
this paper, the first in a series of three reports, is to provide mechanics insights to questions raised by Dr.
George McDonough [3] on aluminum welded joint behavior beyond the elastic limit.
The modified aft skirt structure of the solid rocket booster (SRB) was analyzed to predict safety
margins using updated launch pad loads. Detailed global and substructural models were developed using
a finite element method (FEM). The critical area was identified to be the aluminum weld joining the shell
and a holddown post forging, because the weld material had a lower yield point and ultimate strength
than adjacent parent metals. The weld was modeled with brick elements, five across the width, and the
FEM code iterated the inelastic material properties in a piece-wise-linear routine [4]. While the model
predicted positive margins on the ultimate, the structural test article failed at the weld interface 8 percent
below the required safety factor and at half the expected elongation. Twenty—four weld specimens were
cut from the remaining skirt structure and uniaxially tested. All specimens were noted to fail at weld—
parent interfaces. Average tensile design properties were reported and are included in Appendix A.
File | Action |
---|---|
NASA-TP-2935 Weld Stresses Beyond the Elastic Limit.pdf | Download |
Comment On This Post