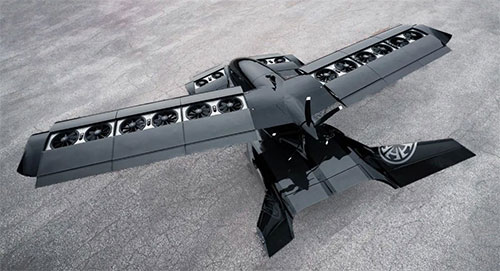
I really don’t like to single out individual programs but this one has long been one of my favorites in terms of impracticality, complexity and sheer chutzpah.
All of what follows is nothing but my opinion with all the normal biases, probable errors and caveats.
This is the project: The aircraft
This project is not unique and displays a lot of the issues that other eVTOL programs also face.
These are the specifications:
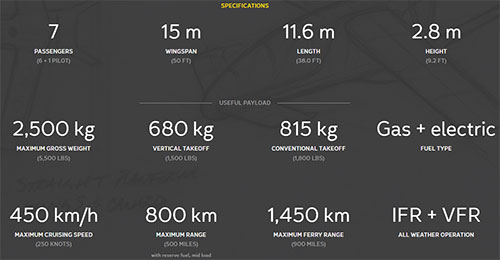
And these are the patents:
https://patents.google.com/patent/US11548621B1/
https://patents.google.com/patent/US11001377B1/
https://patents.google.com/patent/USD997836S1/
Lets do a quick configuration level summary:
Quick configuration level Summary
The aircraft is a twin tail, high wing, canard, single engine pusher monoplane.
The wing has a moderate forward sweep and no taper, the canard has a moderate aft sweep and no taper, the twin tails are more traditional tapered and swept and have a significant outboard cant.
There is a horizontal deck between the fins aft of the cabin and the propeller.
You can see more information here: https://www.youtube.com/watch?v=Es3FmLCcn2M
Their Youtube channel is here Horizon Aircraft – YouTube and you can see they have a scale model flying in a hover.
General configuration summary (considering conventional forward flight only):
It is unclear if any other project has ever combined a canard, a forward swept wing with a laterally spread V-tail. This raises concerns about potential undesired stability and handling characteristics that could be discovered during conventional flight testing.
The lift fans are embedded in the wing and canard. The leading and trailing edges of the wing and canard are movable so the wing can be closed up and present a clean aerodynamic surface for cruise flight.
What happens to a fixed wing aircraft when you add VTOL?
When you add eVTOL to an aircraft flight envelope there are two new district phases of flight that you have to manage; hover and transition. In these two new phases of flight you have to be able to control the aircraft in a way that feels natural and logical to the pilot.
For example, aircraft control surfaces only become effective over a certain speed – for most aircraft of this class this is around 40-50knots. (vast generalization, I know)
In Hover and transition, or until you get to the aircraft stall speed in the transition configuration you will have aero or reduced effectivity from your control surfaces.
One way to remedy some of these problems is to put the tail control surfaces in the wash of the propeller, if you can get some moving air over the tail control surfaces independent of the forward velocity of the aircraft you will have pitch and yaw control and two thirds of your problems are solved.
Some data on propeller slip stream modeling, taken from the excellent paper here (PDF) Propeller Slipstream Model for Small Unmanned Aerial Vehicles (well worth a download and a read through)
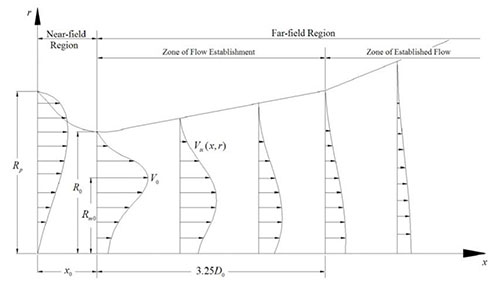
The eagle eyed amongst you will have noticed that the Cavorite X7 with what appear to be elevators on the canard and the widely spaced canted vertical tails have kept the pitch and control surfaces well clear of useful air the propeller generates. This does not mean that they do not have pitch and yaw control in hover and transition, but that they have to design and install additional systems to achieve those same controls.
To paraphrase the redoubtable Bill Lear – the most reliable system is one that you don’t put on the aircraft.
VTOL – how is that going to work?
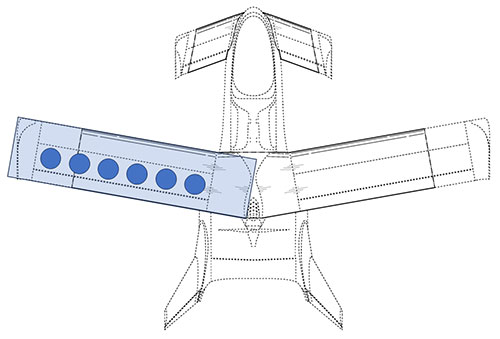
The total disk area does not look large.
I scaled the plan views of the aircraft and came up with a 310sqft wing area – this is very high (this will translate to a high gust response and a rough ride for the passengers at 250knots).
From this we can estimate further that the fans have a diameter roughly 2.25ft and with 12 of them a total of 47.5sqft total disk area – this gives a disk loading of 5500 / 47.5 = 115.8lb/sqft
Using one of my favorite graphs and assuming some rational partial duct efficiency you get a installed power loading of around 1.5lb/hp
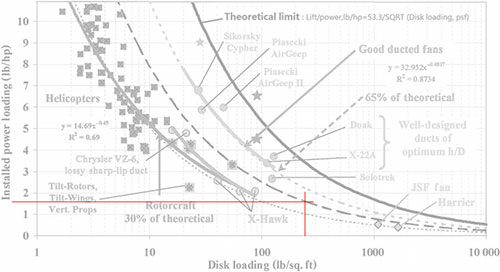
This means that this aircraft will need about 5500/1.5 = 3666HP or around 2.7MW. This number does not look too far out as the AW 609, which also weighs 5500lb (AgustaWestland AW609 – Wikipedia) requires 2 x 1940HP (1.4MW) – a total of 2.8MW, approximately the same power as my scratch calculation. The AW609 looks like it has a higher rotor area and therefore a lower disk loading than the Cavorite X7 which means I am being optimistic for the X7, but lets leave it where it is.
Assuming that the ICE component of the hybrid power system is sized for cruise it follows that hovering will be done from batteries. Assuming an installed weight of 170 wh/kg and a hover of a total of one minute per flight (ignoring all reserves and go around requirements) the battery weight required is around 580lb.
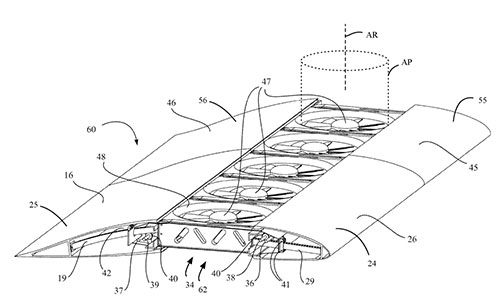
If we assume each motor provides 1/12 of this power this will be 225KW per motor, assuming a motor power to weight ratio of 9KW/kg the weight of each motor will be 25kg or 55lb, as there are 12 motors the total weight of the motors will be 660lb.
If the ICE is required to provide cruise power and the aircraft will cruise at the same speed as the Piper M500 we can assume it will require roughly the same engine (this is not really true as cruise power requirement is less than takeoff power for a conventional aircraft, but the transition thrust requirement for this aircraft will be high – see later section – so we will keep the power the same as the M500) – that is a 500HP Pratt & Whitney PT6A-42A, this will have a wet installed weight of around 310lb.
The ICE engine will need a generator and a motor for the propeller, assuming the same power to weight ratio as the lift motors, the total weight of the generator and the motor for the cruise propeller will be 181lb.
I am going to add 15% of the total motor weights for power electronics and wiring.
I am guessing at the total weight of the single propeller and 12 fans to be 150lb.
Batteries | 580lb |
Lift Motors | 660lb |
Generator and Cruise motor | 181lb |
Power Electronics and Wiring | 126lb |
ICE Engine | 310lb |
Weight of propellers and fans (estimate) | 150lb |
Total | 2007lb |
That is 2007/5500 = 36.5% of the aircraft gross weight, this website (Horizon Aircraft Cavorite X7 (concept design)) reports the empty weight with fuel as 4001lb, assuming the empty weight without fuel is 3300lb (my guess at 700lb of fuel) the aircraft power system consumes 2007/3300 = 61% of the aircraft empty weight.
From Roskam for ‘legacy’ twin engine fixed wing aircraft of this weight class the typical proportion of the powerplant weight to gross weight is 22% to 26% – this is for piston engines. For a modern turbine single, for example the Explorer 500T (Explorer Aircraft), the weight of the installed engine and propeller is close to 10% of the aircraft MTOW.
Bear in mind that this weight assumes 1 minute of hover per flight. Considering reserves and an aborted landing/go-around capability that one minute of time could easily double or triple and the battery weight double or triple along with it…..this is ignored in the numbers above.
Also, in order for the aircraft to be safe and controllable in hover you require a thrust load above the gross weight of the aircraft, so the total available thrust should be, say 1.2 x the aircraft gross weight. This effect is also ignored.
This means that there is not enough weight in the budget for the rest of the aircraft, especially an aircraft with a wing of this size. There is at least 1000lb of mass that would usually be used for the rest of the aircraft (structures, systems, interiors) that has to be dedicated to the propulsion system. This is not a marginal problem and is a fundamental problem with this configuration. 1000lbs of mass is the equivalent of 5 passengers.
Transition – getting from vertical to horizontal
I have worked on a ‘lift fan in wing’ configuration and there is one problem that you don’t realize exists until you sit down and do all the math.
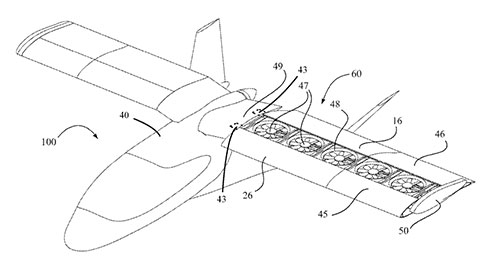
In order to transition you need to get the aircraft moving through the air above its stall speed.
With the upper and lower surface of the wing disrupted by the lift fans your stall speed is higher because of the reduction in wing lift of the broken surfaces.
Because of the higher drag of the aircraft in the lift configuration you require more thrust than you would like. This drag is generated by the geometry of the broken lift surfaces but there is also a drag effect of the column(s) of lift air.
So you will have to fly faster to get to a higher stall speed than a conventional aircraft and you require more thrust to get there quickly enough to keep the battery weight even remotely bearable.
This aircraft has a very large wing for the gross weight so this will help with this problem. I assume they can close sections of the wing skins over the lift fans in sequence to slowly transition lift from fans to wing. However until a wing skin section is closed that section of wing is not really going to generate any lift. So if the LH and RH inboard wing panels close first the rest of the wing (⅔) will need to generate more direct thrust lift per motor and so the weight of the motors will be higher than noted above.
It will be interesting to see how long the aircraft takes to transition and how much forward thrust is required.
This looks to be complex enough that it will have to be controlled by software – there are too many factors to manage for a human pilot so the stability and control of the aircraft in the transitioning state (as well as dealing with failure modes) will have to be software controlled.
Software control of this type, with no consideration of any other costs, generally takes at least $100M USD to develop and certify. Because of the unique nature of this aircraft the final cost of the software could be many times the minimal estimate above.
Lots of moving parts means lots of fun!
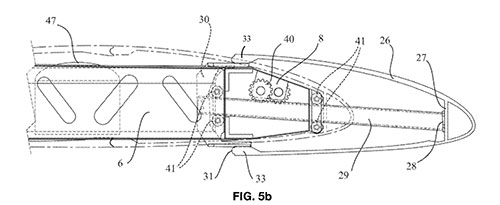
The mechanism for the movement of the leading and trailing edges (from one of the patents) appear to be two cogs that operate on the upper surface of a track that I assume has a series of indentations to match the teeth of the cog.
Right away I can see problems and improvements here. This type of design will be particularly prone to jamming due to foreign objects (grit, for example) coming to rest in the upwards facing indentations.
This problem could be partially mitigated by moving the indentations to the lower surface of the track and placing the cog underneath. In addition, wet lubricant would have to be avoided and this could encourage foreign bodies to get stuck even with the downwards facing indentations so a dry lubricant would have to be used.
It would be better to follow a more traditional actuation and tracking system for flaps and slats, there are some examples shown here 22.16.4. Leading and Trailing Edge Devices – Abbott Aerospace UK Ltd
It also looks impossible to qualify this aircraft for FIKI (flight into known icing) as problems of installing an anti ice system and the potential ice accumulation on these moving surfaces preventing proper operation looks severe.
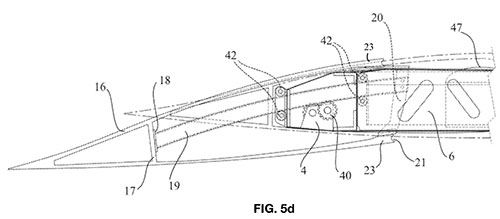
Power Loss
It is not clear what will happen to the aircraft if there is a power failure during hover or transition. Let me correct that, it is very clear what will happen to the aircraft if there is a power failure during hover or transition – it will turn into an expensive non-flying brick. It is not clear what the mitigation is for the power loss scenario.
Tardis?
With ICE hybrid power systems you need to provide internal volume and enclosures that satisfy installation, service and certification requirements for all the various components of the system. In addition the Cavorite X7 has no volume for fuel inside the wing. All of this stuff will have to live inside the fuselage volume – The batteries, the fuel, the ICE engine, power generation system and the power electronics. As the aircraft cruises at 250knots (Because of the large transparencies I am assuming that this aircraft is non pressurized, cruising at 250knots at below 8000ft with a wing this large is going to consume a lot of power – but that is another issue) I assume the landing gear will have to be retractable and so the landing gear also has to share this space. As do the 7 occupants.
In addition to this the liquid fuel has to be kept at, or close to the Center of gravity otherwise the excessive pitch caused by the change in fuel mass throughout the flight will require an oversize pitch trim system – and an oversize trim drag which will hurt cruise performance.
The sleek lines of the Cavorite X7 do not give much of a clue where all of this stuff (propulsion, landing gear, people) will fit.
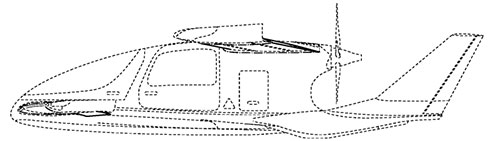
Technical Summary
So – mostly bad news.
There appear to be several ‘marginally’ viable technical aspects to this configuration. Considering the power requirements, the weight of the propulsion system is excessive for the gross weight, especially in the context of the desire to carry 7 occupants. This is a configuration that from a mass properties perspective appears to be unachievable.
The total transition sequence is over complex and the thrust power requirements are high. The requirement for software control makes this design very expensive to get to market.
There is no clear mitigation of critical failure modes such as loss of power. In addition the amount of failure modes are very large due to the number of moving surfaces and the number of lift fans. If this is all mitigated by software – yikes.
The fuselage does not appear to be designed with the necessary volume for all of the systems required for the aircraft to fulfill its advertised mission.
The Inevitable Financials
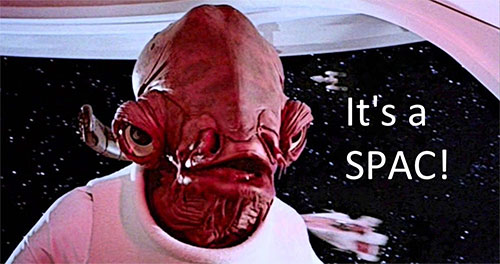
So why have I looked at this aircraft now? Well……..just before Christmas I noticed that they had floated on Nasdaq via a SPAC. New Horizon Aircraft Ltd. Class A Ordinary Share (HOVR).
Companies with no product on the market making a public offering of their equity is a confidence game in the real sense of the word. The value of the company can only be based on the confidence that the company will end up being financially viable at a later date. The market is showing little confidence that there will be a successful outcome at this time.
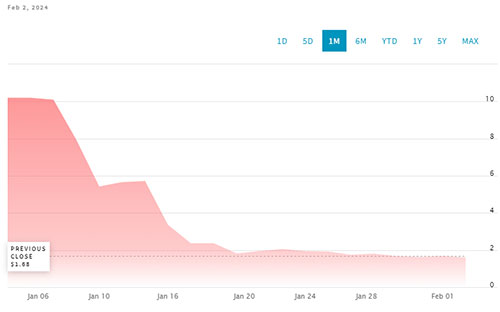
In just a month the shares are trading at close to 15% of the original offer price. Not a stellar performance (sarc). To understand the nature of SPACs and their inherent problems this is a good article: SPACs: What You Don’t Understand Can Cost You Money
So – this program is illustrative of the eVTOL ‘boom’. It is complex, impractical and has many, many factors stacked against its eventual commercial success. Horizon has floated on the stock market and as they have not dedicated the large amount of capital and effort needed to buoy confidence on an ongoing basis (Iike Joby and Archer) they have suffered the inevitable consequence.
In order to succeed they will have to invest enormous amounts of capital in the aircraft development and certification and overcome and mitigate all of the problems inherent in their choice of configuration. They will also have to devote additional time, capital and effort into building the confidence that this is possible and they are on the path to achieve their goal.
Comment On This Post