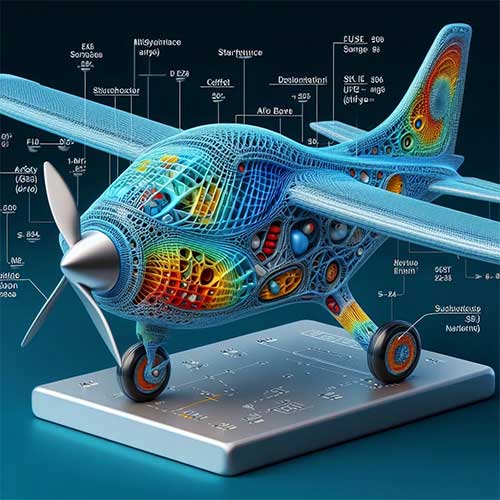
https://www.easa.europa.eu/en/downloads/116479/en
I am getting into the subject of FEM validation with one of our clients. Finite element methods have been used in aerospace development for over half a century and are not new. So why has the FAA decided that a formal validation of finite element models is required now?
Let’s remind ourselves of how this used to work. Finite element modeling was one of a set of tools available to the analyst. From hand analysis to more complex excel, mathcad or matlab models and the linear and nonlinear finite element models.
All these methods were used at the discretion of the engineering organization and subjected to checks and reviews of the engineers and technical management based on their professional knowledge and experience. Where necessary, you would work with a Designated Engineering Representative or a Compliance Verification Engineer to validate to the level necessary for typically only the global finite element model.
Now, any Finite element model requires validation, no matter how simple or determinate.
Some years ago the certification agencies started to get nervous about the integrity of finite element models. The reason for this is not clear. I don’t know if it because of an actual or perceived drop in standards within the industry, an actual or perceived drop in confidence and specific technical competence of people at the FAA or the general creep we are seeing towards the slow adoption of all manner of judgment being transferred from non government entities (me and you) to government entities.
Will it make aircraft safer? – maybe. Will it make the process of development more expensive? – yes.
The problem has been outlined to me during conversations with people who have tried to go through the process already.
The problems encountered go something like this (and I am very broadly paraphrasing):
“The reason that the regulator wants greater oversight over FE modeling is because most people at the FAA do not really understand FE modeling. Getting a detailed plan agreed and approved for exactly how you are going to show validation of your FE models is very difficult and can take a very long time because most people at the FAA do not really understand FE modeling.”
You get into the circular logic of government oversight. The government wants more oversight because they do not trust you because of their lack of knowledge and experience. The oversight process is difficult and expensive to complete because the people at the government do not have the necessary knowledge and experience to make a decision.
Those of us in the engineering community know that hand analysis methods for load distribution and failure mode prediction have a set of issues and problems and that finite element models for load distribution and failure mode prediction have a different set of problems. This is why the unlimited use of any methods by a professional engineer subject to check and approval by their industry peers and betters is the best approach to take.
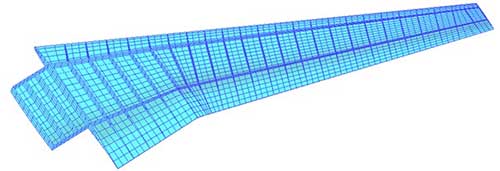
I am curious how far this creep is going to progress. If the regulator is getting nervous about FE models, I can’t wait to see the reaction when they find out how inaccurate hand analysis methods can be.
I wonder how long it will be before we have to validate all analysis methods to government controlled standards. Imposed with the best of intentions but without any nuance, wisdom or professional volition.
The way this is imposed as a mandatory element of the power of the regulator is not through law, or regulation, or advisory material, or policy, but through DER training.
This is an increasing problem. You will have noticed that the adoption of the ASTM standards have created a set of absolutely and definitely non mandatory proprietary commercial standards as the only possible way of certifying to part 23 regulations. In this way government departments can create what are in effect absolutely mandatory rules, not by changing the statue or even regulations but by using methods with much less consideration and accountability.
The regulator is now using DER training to create mandatory rules. Just like ‘independently developed industry standards’ (chuckle) such as the ASTM standards can have the weight of law, now DER training carries the mandate of statute.
Those who pay attention may have observed a gradual erosion of what were once cherished freedoms, now replaced not by statutory restrictions, but by rules masquerading as law, crafted within government departments without any accountability.
At least with the conversion of part 23 from open regulations into a horribly flawed pay to play system there was lip service to a public consultation process. The majority of the comments in the process which were against the change were completely ignored, but at least there was the fig leaf of a rushed and entertainingly pointless consultation process.
Using DER training is a new, much quicker and efficient process of creating mandatory rules without all that tedious mucking around in the actual rulemaking process
The links at the start of this document lead to the training and guidance material. The information in this guidance material is excellent and I have done similar studies on the different outcomes of different modeling methods, as a lot of other engineers will have as well. We are all naturally curious and want to understand the methods and techniques we employ.
But no need to worry! The government has done all of the curiosity for you and all you have to do is relax and comply to your heart’s content.
Will engineering be spending significant additional time to write detailed validation plans and enter negotiations with the regulator until those validations have been approved and then spend additional time to nuance FE models to strain gage results so they match close enough to satisfy the plan? Absolutely!
Anyone who has done a lot of testing will know that strain gauge results come with accuracy problems all their own – there is some good information here on the accuracy of ideally installed gages https://www.omega.co.uk/techref/pdf/straingage_measurement.pdf
The engineer has the challenge of selecting strain gage locations for correlation that meet the following criteria:
High enough strain to be read accurately
Low strain gradient
Accessible to allow gage installation
The engineer then has to pray that the gauge is installed correctly (perfectly) and endures for the duration of the test program giving perfect results.
The guideline is that deflection has to match with 5% and strains have to match within 10%
If the structural means of compliance depends on the FE model, failure to validate the FE model means that you do not get your type certificate.
The other amusing part is that if you fail to validate your model you are not allowed to improve your model and then show validation. Within the compliance process there is no possibility of improving the model, it is a one shot pass/fail single event.
Also, bear in mind that the FE model validation standards are to be applied regardless of the performance level and complexity of the aircraft. If you are dealing with a small stiff composite aircraft that does not allow buckling up to ultimate level that is inherently easy to predict, you are forced into the same level of validation as a non linear, buckling transport category aircraft.
When all you have is a hammer everything looks like an expensive compliance exercise of dubious value.
Comment On This Post