naca-report-224
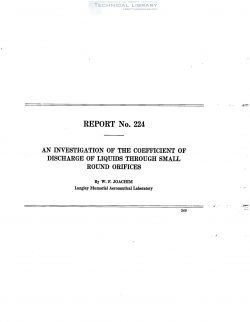
- Version
- 172 Downloads
- 698.90 KB File Size
- 1 File Count
- August 25, 2016 Create Date
- August 25, 2016 Last Updated
National Advisory Committee for Aeronautics, Report - An Investigation of the Coefficient of Discharge of Liquids Through Small Round Orifices
The work covered by this report was undertaken in connection with a'general investigation
of fuel injection engine principles as applied to engines for aircraft propulsion, the specific
purpose being to obtain information on the coefficient of discharge of small round orifices suitable
for use as fuel injection nozzles.
Flow of the liquids tested under high pressure was obtained with an intensifier consisting of
a 5—inch piston driving a direct connected %-inch hydraulic plunger. The large piston was
operated by compressed air and the time required for the displacement of a definite volume by
the hydraulic plunger was measured with an electrically operated stop watch. The coefficients
were determined as the ratio of the actual to the theoretical rate of flow where the theoretical
flow was obtained by the usual simple formula for the discharge of liquids through orifices.
Values for the coefiicient were determined for the more important conditions of engine
service such as discharge under pressures up to 8,000 pounds per square inch, at temperatures
between 80° and 180° F. and into air compressed to pressures up to 1,000 pounds per square
inch. The results show that the coefiicient ranges betwaen 0.62 and 0.88 for the different test
conditions between 1,000 and 8,000 pounds per square inch hydraulic pressure. At lower
pressures the coefiicient increases materially.
It is concluded that within the range of these tests and for hydraulic pressures above 1,000
pounds per square inch the coefficient does not change materially with pressure or temperature;
that it depends considerably upon the liquid, decreases with increase in orifice size, and increases
in the case of discharge into compressed air until the compressed-air pressure equals approxi—
mately three-tenths of the hydraulic pressure, beyond which pressure ratio it remains practically
constant.
File | Action |
---|---|
naca-report-224 An Investigation of the Coefficient of Discharge of Liquids Through Small Round Orifices.pdf | Download |
Comment On This Post